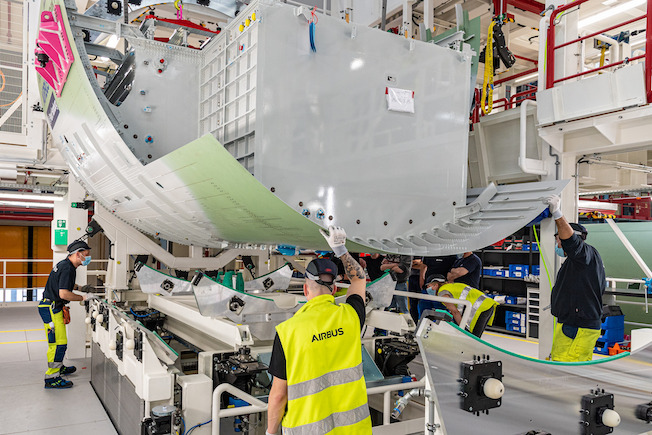
Airbus
Airbus teams have reached a significant milestone in the making of the first A321XLR – production has started in Germany with the structural assembly of the Centre and Rear fuselages.
In May, Airbus’ manufacturing partner Premium AEROTEC delivered the first fully equipped Rear Centre Tank to Airbus’ major component assembly facility in Hamburg – a key component of the A321XLR’s performance. Heralding the start of the assembly of the aircraft’s rear fuselage and the centre fuselage in the dedicated “Structure Pilot Line”.
We are on TELEGRAM. Click and follow us: t.me/aerotendencias
“It’s a major milestone for the A321XLR programme. The teams can be proud of this achievement and the overall speed of industrialization. We are on track with our planning. The pilot line dedicated to the A321XLR is ready and waiting to operate the assembly phases for the first flight test aircraft, all the way through to the entry into service, ” said Martin Schnoor, Head of A321 XLR Programme Development Airframe Programme.
The Rear Centre Tank, the XLR performance masterpiece
The Rear Centre Tank (RCT), which is unique to the new long-range A321XLR, is a permanently installed high-capacity fuel tank that makes maximum volumetric use of the aircraft’s lower fuselage. Integrated in fuselage Sections 15 and 17 and located behind the main landing gear bay it holds up to 13,100 litres, which is more fuel than several Additional Centre Tanks (ACTs) combined could previously hold in the A321 aircraft Family.
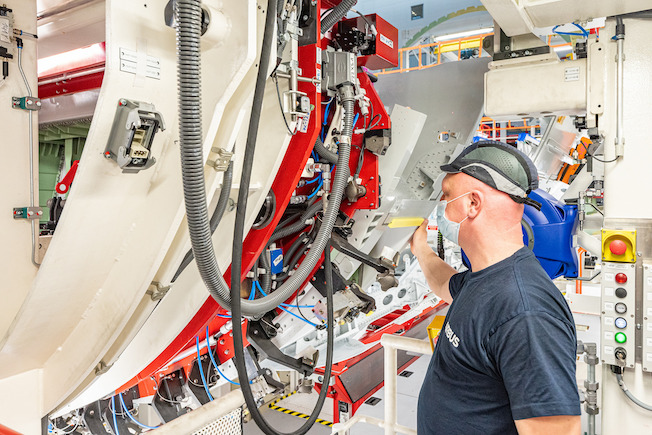
Airbus
Overcoming the covid challenges
The integration of the RCT represented a significant challenge for the teams to ensure the smooth integration of the new rear centre tank and its new fuel systems. Operations faced a very tight time schedule for the overall development and the industrial set-up. Around this time, the COVID-19 pandemic started to impact collaborative work on the XLR plateau.
“It was yet another significant challenge, but we quickly adapted using digital means with a “co-design approach” to achieve a solution for the aircraft,” said Stephan Meyer, Head of A321XLR Industrial Centre Aft Fuselage. “We are proud of this great product, developed and industrialized under such difficult circumstances, which is well underway,” he concludes.
The assembly phases on the pilot line
In parallel to this, the structural assembly of Section 15 started in mid April with the integration of the shells from the supplier RUAG, the Centre Wing Box coming from Airbus Nantes, and the keel beam and Rear Flange Module supplied by Premium AEROTEC. All parts of the integral Rear Centre Tank coming harmoniously together.
These major sections are currently assembled on the new dedicated production line in Hangar 260 – a pilot line deliberately separated from the rest of the A320 line, to be able to start the ramp-up of the A321XLR’s fuselages without impacting Hamburg’s existing single-aisle production. The pilot line itself has been fully designed in 3D, allowing for smart integration of the A321XLR design data from the beginning. “The coherent 3D design enabled optimum development of the overall A321XLR’s industrial system,” explained Stephan. “In addition we were able to validate the design digitally taking account of ergonomics, operations and logistics beforehand,” he concludes.
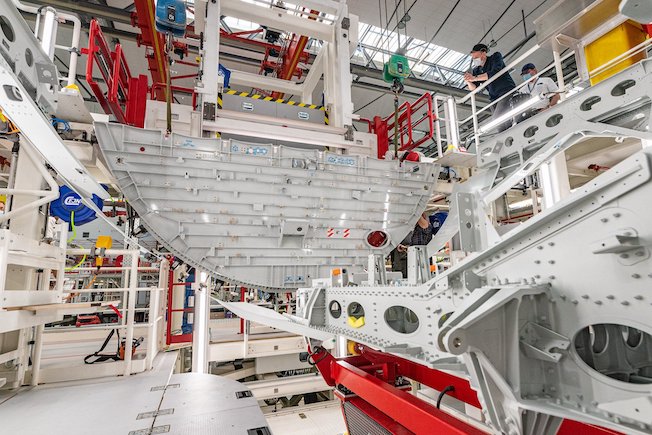
Airbus
Making it happen
In the coming weeks, the teams will finalize the integration of the RCT module into section 17, with the structural assembly of the second flight test aircraft. The equipment assembly phase of the first aircraft is planned in the autumn, followed by a dedicated period for flight test equipment installation.
The A321XLR is a further step in the evolution of the Airbus’ single-aisle family and has been designed to maximise overall commonality with the rest of the Family. While at the same time introducing minimal changes needed to give the aircraft an Xtra Long Range, increased revenue payload, and the best travel experience as a result of the Airspace cabin.
This aircraft will provide airlines with a range of up to 4,700nm and a 30% lower fuel burn and CO2 emissions per seat compared with previous-generation aircraft.
The entry into service is planned in 2023.